Get Smart with Your Water Usage: Three Tips from Our Mid-Sized Operation
Water is the most plentiful natural resource on the planet. However, our world doesn’t always treat it as such. When it comes to operating an environmentally friendly hog farm, it is essential to respect water for the precious commodity that it is. By doing this, hog farms and facilities that play a role in every stage of the growing and harvesting process can be both positive contributors to their community and profitable.
When I started at Premium Iowa Pork (PIP) and Premium Minnesota Pork (PMP) over a decade ago, Lynch Family Companies Chairman Gary Lynch and I agreed that our Hospers, Iowa facility, which only processed about 2,200 head per day, did not have the ability to compete with larger operations. To set us apart, we decided to focus on antibiotic-free pork production. Making this change positioned us with an opportunity for improved profitability – becoming a key player in the niche market that produces the majority of the 3% of antibiotic-free pork in the U.S. However, the uniqueness of our product exposed us to increased production costs – further elevating our need to reduce water usage at our facilities.
Iowa’s meat producers know better than anyone that “green” ag practices have been around for as long as farming itself. By nature, we are good stewards of the land and our animals. As concerns about the global environment grew in the 1970s, so did the industry’s efforts around telling our story of commitment to sustainable practices. For PIP and PMP, water seemed like a great place to start.
While it remains inexpensive to buy water, today’s real expense comes from treating it to meet the standards set forth by local, state and federal regulations before it goes back to the larger water supply. Here are a few tactics that helped us achieve water conservation success that will likely work on your facility:
1. Build relationships with local leaders to tackle water challenges together.
The first issue that we needed to address was how our community has a very small population, and the size of the city’s water treatment plant was designed to fulfill only the small needs of their residents. That forced us to truck much of our water to a different location to be treated, which was a financial burden. Because of this, we worked with the mayor, the city council, and the treatment plant by providing financial support to help double its size to accommodate our current and future water needs. This was important as our operations were growing and we’re now processing 3,100 head per day.
2. Assess your water usage and identify areas of improvement.
It’s important to constantly be asking the following question of where, why, and how much water is being used at your farms and facilities.
To alleviate concerns over excessive usage in our scalding and dehairing operation, both of which are prime opportunities for water waste, we use a non-traditional system to reduce water usage. l. When it comes to activities like cleaning a carcass, water pressure is much more important than volume, so we installed restrictors and use specialized spray heads.
Then, we built it into the orientation efforts of all new employees to emphasize how important proper water usage is to everything we do. Even the third-party contractors who clean our buildings every night are required to use water as efficiently as possible. We also track usage with water meters throughout the facility.
3. Invest in technology and tools that will help you achieve your water-saving goals.
After the water is through the plant process but before it reaches the municipality, it is pre-treated. That process consists of a screen to remove larger particles from the screen. It is then processed through a dissolved air flotation (DAF). The process uses microscopic bubbles to float the solids and grease to the surface to be removed by a skimmer. The removal of this material helps to remove the TSS, BOD and oil and grease in the water, which vastly reduces the pollutant load.
Finally, we used a Moving Bed Biofilm Reactor (MBBR) to remove the micropollutants that remain in the water. This is a process where biofilm essentially eats the remaining microscopic material in the water. These processes, when combined, are an extremely effective method of removal and result in an approximately 95% reduction of pollutants through the processing of our animals. The water is then sent to the municipality for final processing.
FINAL THOUGHTS
Regulations are stricter than ever for our industry as we serve a customer base that increasingly demands transparency in how the food they eat gets to their table. Getting smarter about your water usage is a great way to reduce costs while maintaining deep-rooted commitments to sustainable ag practices.
View Lynch Family Companies’ 2022 Stewardship Report for more information on their commitment to sustainability and the importance of reducing water usage at facilities.
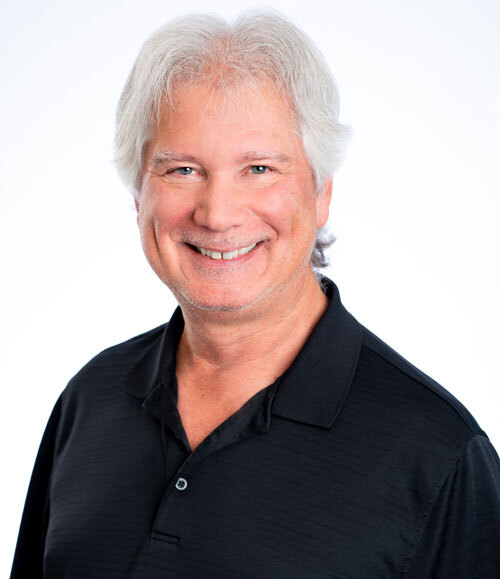
About Dan Paquin
Dan Paquin has dedicated his life to the pork industry and has served as president of Premium Iowa Pork (PIP) and Premium Minnesota Pork (PMP) for 11 years. His experience in the industry and commitment to meeting consumer demands inspired him to grow his companies’ footprint in the crate-free, antibiotic-free fresh pork market. Today, PIP and PMP produce a majority of the 3% of crate-free, antibiotic-free pork in the U.S. Prior to his current role, Dan started his professional career as an hourly employee with the goal of becoming a utility butcher and later joined management teams at Swift and Co., FDL Foods, IBP, Inc. and John Morell/Smithfield Foods.